What is Porosity in Welding: Usual Resources and Efficient Treatments
What is Porosity in Welding: Usual Resources and Efficient Treatments
Blog Article
The Science Behind Porosity: A Comprehensive Overview for Welders and Fabricators
Understanding the elaborate systems behind porosity in welding is vital for welders and makers making every effort for impeccable craftsmanship. From the composition of the base materials to the intricacies of the welding process itself, a wide range of variables conspire to either intensify or ease the visibility of porosity.
Recognizing Porosity in Welding
FIRST SENTENCE:
Examination of porosity in welding discloses critical understandings right into the stability and quality of the weld joint. Porosity, characterized by the visibility of dental caries or spaces within the weld metal, is an usual problem in welding processes. These gaps, otherwise effectively resolved, can endanger the architectural integrity and mechanical residential or commercial properties of the weld, resulting in potential failings in the completed product.

To find and quantify porosity, non-destructive screening approaches such as ultrasonic testing or X-ray inspection are usually used. These methods allow for the recognition of internal issues without endangering the integrity of the weld. By analyzing the dimension, shape, and circulation of porosity within a weld, welders can make educated choices to enhance their welding processes and accomplish sounder weld joints.
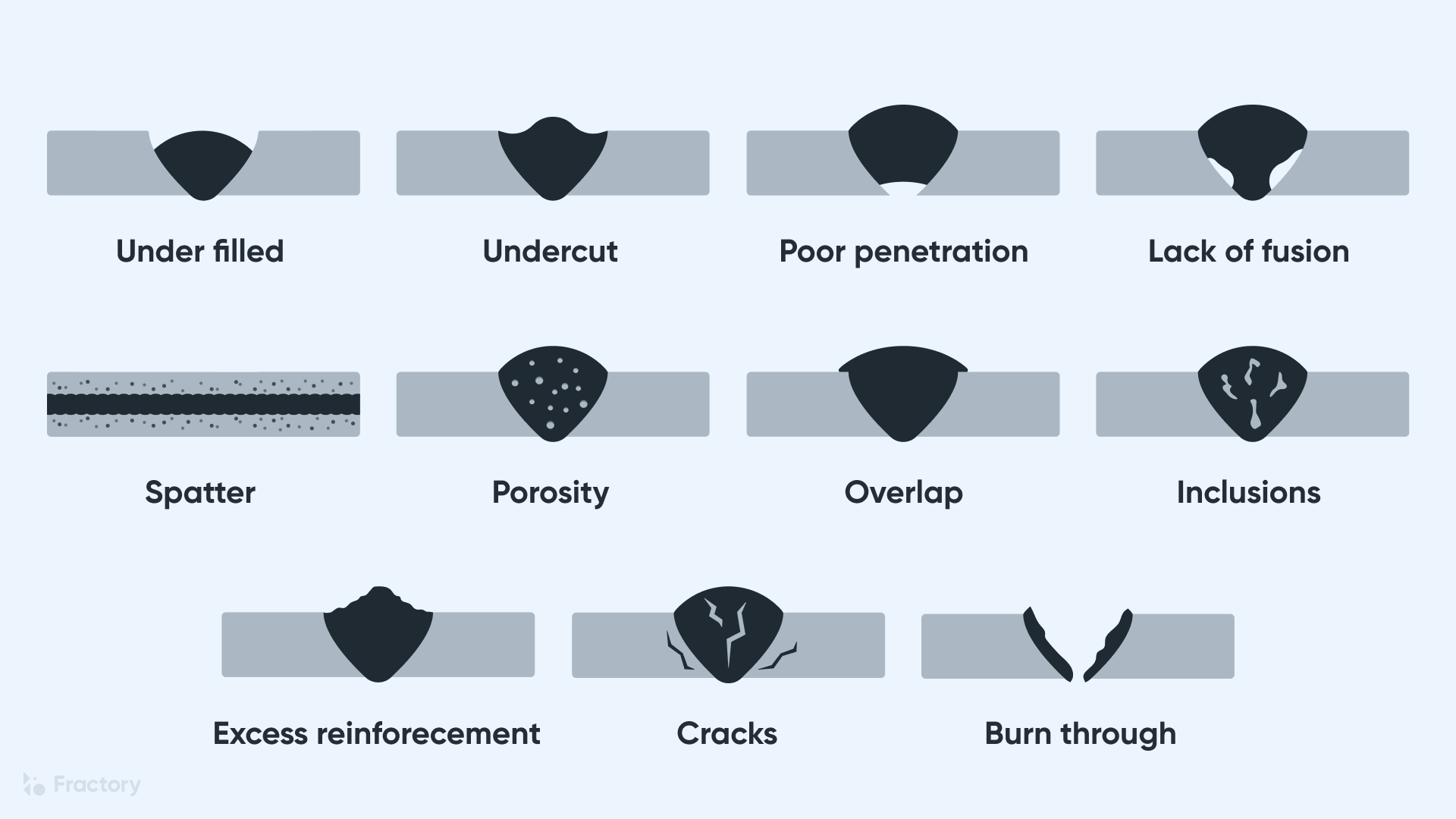
Factors Affecting Porosity Development
The event of porosity in welding is affected by a myriad of aspects, varying from gas shielding performance to the complexities of welding parameter setups. Welding parameters, including voltage, present, take a trip rate, and electrode type, likewise effect porosity development. The welding technique employed, such as gas metal arc welding (GMAW) or protected steel arc welding (SMAW), can affect porosity formation due to variations in warm circulation and gas insurance coverage - What is Porosity.
Effects of Porosity on Weld High Quality
The existence of porosity also weakens the weld's resistance to deterioration, as the caught air or gases within the voids can respond with the surrounding atmosphere, leading i thought about this to degradation over time. In addition, porosity can impede the weld's ability to withstand stress or impact, more endangering the overall top quality and dependability of the bonded framework. In crucial applications such as aerospace, auto, or structural constructions, where safety and security and resilience are paramount, the damaging effects of porosity on weld high quality can have severe effects, emphasizing the relevance of reducing porosity via appropriate welding strategies and procedures.
Strategies to Reduce Porosity
In addition, using the appropriate welding specifications, such as the right voltage, existing, and take a trip rate, is crucial in avoiding porosity. Preserving a constant arc length and angle throughout welding likewise assists lower the chance of porosity.

Furthermore, selecting the right shielding gas and maintaining proper gas flow rates are i loved this important in reducing porosity. Utilizing the suitable welding method, such as back-stepping or utilizing a weaving motion, can also assist distribute warm evenly and decrease the chances of porosity formation. Ensuring correct air flow in the welding atmosphere to remove any possible resources of contamination is important for achieving porosity-free welds. By implementing these strategies, welders can properly lessen porosity and create top quality bonded joints.

Advanced Solutions for Porosity Control
Implementing innovative innovations and ingenious techniques plays an essential role in attaining remarkable control over porosity in welding processes. In addition, employing innovative welding techniques such as pulsed MIG welding or changed atmosphere welding can additionally help minimize porosity issues.
An additional advanced option involves using innovative welding equipment. As an example, utilizing devices with integrated features like waveform control and sophisticated power resources can enhance weld high quality and reduce porosity dangers. Moreover, the implementation of automated welding systems with accurate control over specifications can dramatically reduce porosity flaws.
Furthermore, integrating sophisticated surveillance and examination technologies such as real-time X-ray imaging or automated ultrasonic testing can help in finding porosity early in the welding procedure, enabling prompt corrective actions. Overall, integrating these advanced services can considerably enhance porosity control and improve the general high quality of bonded elements.
Final Thought
In verdict, recognizing the scientific research find out behind porosity in welding is crucial for welders and makers to generate high-quality welds. By recognizing the elements affecting porosity development and applying strategies to decrease it, welders can boost the general weld high quality. Advanced services for porosity control can even more enhance the welding process and make certain a solid and trustworthy weld. It is necessary for welders to constantly inform themselves on porosity and execute best techniques to attain ideal results.
Report this page